In order to avoid problems with slugs, the use of a "slug catcher" is deployed. Located between the process equipment and the pipeline outlet, slug catchers are vessels with enough holding capacity to hold a slug as they travel down the pipeline. The additional holding capacity allows for the gradual draining of liquids from the system to avoid system overload.
MONITORING SLUG CATCHER LEVEL
The biggest problem for slug catcher applications is solids accumulation. The build-up occurs naturally during normal operations. Solids will continue to accumulate until they are physically removed.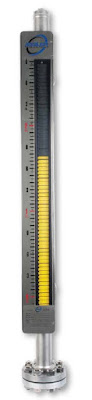

The most common liquids measured are hydrocarbons and water. Once the sight glass accumulates solids or discoloration on the viewing window, the liquids may not be visible at all.
MAGNETIC LEVEL GAUGE
To overcome all of the challenges that slug catcher applications pose for safe and reliable level monitoring, Jogler engineers created the following design that has been implemented and proven over many years of operation:INDIRECT LEVEL MEASUREMENT
Unlike a sight glass, a magnetic level gauge does not include direct sight of the liquid. Instead, the level is magnetically conveyed via the interaction of flags in the external scale assembly and magnets in the float. This makes it impossible for the glass to become clogged or dirty. Therefore, a magnetic level gauge offers constant, unimpeded liquid level viewing that will not deteriorate with any solids accumulation.

GUIDE RODS
To prevent solids from interfering with proper operation of the float, the chamber is made from a 3” pipe with a 2” or 2.5” float and guide rods (other configurations available). This allows space for the solids to accumulate without interfering with the float traveling.

To help avoid buildup, the float and internal chamber can be coated with various products, such as Teflon S, to prevent fouling buildup on the float. If buildup can occur on the float, the weight of the float will increase give false low level readings.
CUSTOM FLOATS
An important part of the function of a magnetic level gauge is the design of the internal float. Floats can be engineered to handle various liquids, including extremely light hydro-carbons. To compensate for potential solids build-up, extra buoyancy can be included in the design of a float to ensure it can power through the solids without hanging up.

In some slug catcher applications, iron sulfides and other ferromagnetic particles may be present. These magnetic particles present a risk to the long-term operation of the float, accumulating on the float’s magnets. This can increase the weight of the float causing false low level readings and can even build up to the point where the float sinks or gets stuck. To eliminate these risks, a magnetic particle trap can be installed on one or more of the process connections. The magnetic particle trap consists of high strength super-magnets that are placed in the flow path to the magnetic level gauge. These magnets collect any magnetic particles that can make it to the chamber to protect against build-up on the float. The magnetic particle trap is designed easily be removed from the process connections so it can be periodically cleaned.
HEAT TRACING / INSULATION

For more information, contact Alliance Technical Sales. Call 630-321-9646 or visit https://alliancets.com.