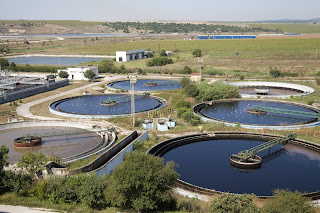 |
Sewage treatment is but one area where water quality measurement is employed |
It would be difficult to understate the role and importance of water in industrial processing, even our own biological existence. In the
first installment of this series, the roles of dissolved oxygen and chlorides were covered.
Continuing the examination of water quality monitoring in municipal and industrial processes, another key variable which requires monitoring for industrial water use is sulfate. Sulfate is a combination of sulfur and oxygen, salts of sulfuric acid. Similarly to chlorides, they can impact water utilization processes due to their capability for corrosion. The power generation industry is particularly attuned to the role of sulfates in their steam cycle, as should be any boiler operator. Minerals can concentrate in steam drums and accelerate corrosion. Thanks to advancements in monitoring technology, instruments are available which monitor for both chlorides (covered in the previous installment in this series) and sulfates with minimal supervision needed by the operator, ensuring accurate detection of constituent levels outside of an acceptable range. Ionic separation technologies precisely appraise the amount of sulfate ions in the stream, allowing for continuous evaluation and for corrective action to be taken early-on, avoiding expensive repairs and downtime.
Another substance worthy of measurement and monitoring in process water is sodium. Pure water production equipment, specifically cation exchange units, can be performance monitored with an online sodium analyzer. Output from the cation bed containing sodium, an indication of deteriorating performance, can be diverted and the bed regenerated. Steam production and power generation operations also benefit from sodium monitoring in an effort to combat corrosion in turbines, steam tubes, and other components. Sodium analyzers are very sensitive, able to detect trace levels.
Ammonia is comprised of nitrogen and hydrogen and, while colorless, carries a distinct odor. Industries such as agriculture utilize ammonia for fertilizing purposes, and many other specializations, including food processing, chemical synthesis, and metal finishing, utilize ammonia for their procedural and product-oriented needs. An essential understanding of ammonia, however, includes the fact that the chemical is deadly to many forms of aquatic life. Removing ammonia from industrial wastewater is a processing burden of many industries due to the environmental toxicity.
Methods for removing ammonia from wastewater include a biological treatment method called ‘conventional activated sludge’, aeration, sequencing batch reactor, and ion exchange. Several methods exist for in-line or sample based measurement of ammonia concentration in water. Each has particular procedures, dependencies, and limitations which must be considered for each application in order to put the most useful measurement method into operation.
As water is an essential part of almost every facet of human endeavor and the environment in which we all dwell, the study and application of related analytics is an important component of many water based processes. The variety of compounds which can be considered contaminants or harmful elements when dissolved or contained in water presents multiple challenges for engineers and process operators.
Alliance Technical Sales specializes in the instruments, equipment, and supplies utilized to analyze water and other liquids employed throughout commercial and industrial operations.