 |
Industrial Thermocouples |
A
thermocouple is a device which functions as a temperature sensor. Two wires, made of dissimilar metals, are joined together at both ends. The thermocouple is, at this point, a thermoelectric circuit with current flowing in relation to the temperature at each junction. The temperature of one junction is known and constant, called the cold junction. The other junction is placed in contact with the media or object to be measured. The closed circuit of the thermocouple subsequently gets broken at the center, and the open circuit voltage from the hot junction is a direct function of the junction temperature. Heating or cooling the sensing junction of the two metals produces a voltage directly correlating to the temperature.
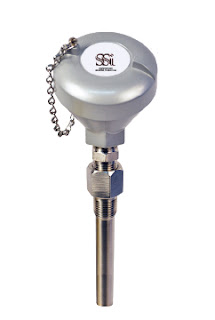
There are a number of metal combinations used to produce
industrial thermocouples. Each combination has a respective set of performance attributes, operating temperatures, tolerances, and cost that may deliver best performance for a particular use.
Common Thermocouple Types and Composition
- Type J (Iron / Constantan)
- Type K (Chromel / Alumel)
- Type T (Copper / Constantan)
- Type E (Chromel / Constantan)
- Type N (Nicrosil / Nisil)
- Type B (Platinum / Rhodium)
- Type R (Platinum / Rhodium)
Generally, thermocouple sensor assemblies, often a tube enclosing the thermocouple junction, can be grounded, ungrounded, or exposed. The wires constituting the tip of a grounded probe are attached to the inside of the probe wall, allowing for maximal heat transfer through the probe wall to the junction while maintaining a physical separation between the junction and the measured media or object. The difference between grounded thermocouple probes and ungrounded thermocouple probes is that in ungrounded probes, the junction is not attached to the probe wall. For this reason, ungrounded probes can exhibit slower response time, but do provide electrical isolation of the junction from the housing. An exposed thermocouple will have the junction protruding from the probe tube or perforations in the tube to allow actual contact between the measured material and the junction. While this provides very rapid response, the junction is exposed to damage and wear.
 |
Various Thermocouple Styles |
Thermocouples are useful for process measurement due to their size, response, ruggedness, accuracy, cost, and wide range of available form factors. Chemical and petroleum refineries, as well as other fluid processing operations, can use multiple thermocouples to control, limit, test, log, and monitor process-related temperatures. Temperature is one of the most measured parameters in industry. Understanding the temperature range being measured, the accuracy level required, and the related process vibration concerns of each industry will aid in selecting the proper thermocouple for an application. When properly matched to the application requirements, thermocouples are a durable and cost-effective process measurement option.
Download your temperature sensor selection catalog here.
Contact Alliance Technical Sales with your temperature sensing requirement. Their application engineers will help you select the best sensor for the job.